15 Oct 2016 - Experience and one Experiment
The dominant purpose of this day's work was to provide an Experiental Archaeology opportunity for a chapter of the SCA. Never giving up an opportunity, however, there was also a small design experiment going on in the background.
Title: A three pronged approach
Series: Matching Archaeology (ÆZ)
Background:
The furnace is based on hearth ÆZ from Ribe - a 30x60cm oval base. For this design the primary air inlet (a standard 2.5 cm I.D. port) was not run all the way through the outer wall. It was instead pushed half way into the wall, and three smaller air ports were put through the inner side of the wall. Since a 2.5cm I.D. inlet has a cross sectional area of 4.9 cm
2, the outlets needed a similar combined volume. This called for 7mm radius for the outlet ports.
Specific Question(s):
- Will a one-to-three air inlet provide enough air to heat the furnace to the required temperatures to work the glass?
- Will the burn pattern on the base, following use, more closely match that seen on the archaeological remains?
Materials:
- Furnace: Cobb (clayy, sand, horse manure, approximately 1/3 of each material)
- Charcoal: Royal Oak (unsized)
- Glass: Standard 104 CE lampworkers glass
- Air source: Hair dryer (0.4 L/m)
Steps:
- Build: Using the cobb mixed build the furnace to shape
- Harden: Allow the furnace to air dry
- Sinter: Using a wood fire, dry the clay, slowly raising the temperature as the water is driven off to sinter the structure to a ceramic
- Preheat: On the day of use - use wood to gently warm the body of the furnace
- Fire: open the top, load charcoal, close the top. Seal the top in place using a clay/water mix. Turn on air.
- Work: At temperature (c. 800C) make the beads.
- Recharge: whent he temperature drops too far to work glass, open the top, refill with charcoal, replace and re-seal the top and start again
- Cool: When work is done for the day allow the furnace to cool
Variables:
The air inlet change was the only difference between this furnace and any number of others we have run over the years.
Observations:
- The hair dryer used for air keep shifting position and had to be re-set to ensure the entire airflow was going into the furnace.
- Ash levels in the beads seemed to be about what we are used to (a lot more than is seen on the artefacts)
- Temperatures in the two chimneys were regularly mis-matched. At different times we could make beads in the left chimney but not the right, both chimneys, or the right but not the left. This would change several times during each charcoal load.
- The entire body of charcoal within the furnace appeared to be engaged rather than just the parts immediately in front of the air vent.
Exterior length of base | 50.8 cm |
Exterior width of base | 27.5 cm |
Exterior height to shoulder | 21.5 cm |
Exterior height to top of chimney | 27 cm |
Access door height above ground | 18 cm |
Tuyere height above ground | 9 cm |
Access door Length | 19 cm |
Access door width | 23 cm |
Chimney distance from end | 12.5 cm, 14.5 cm |
Chimney diameter | 7x6, 7.7x7.5 cm |
External Tuyere Diameter | 2.5 cm |
Internal Tuyere Diameters | 1.6 cm |
Conclusions:
The three prong air inlet system appears to work well. The differing heat in the chimneys can easily be atrributed to different burn rates in the unsized charcoal. The three inlets were not well aligned on the vertical axis. We can likely improve the results through better design of the three-pronged approach.
The burn pattern in the bottom is much closer to the archaeological remains than our previous efforts with air splitters. There are two clear 'white' zones associated with the 'right' and 'center' air inlets. The 'center' one is small and close to the far wall. The 'right' zone spreads across the base from the near to the far side. This matches the physical setup as the 'right' inlet points 'lower'(towards the base) than the 'center' inlet. The 'left' side is a more 'grey' colour but still stands out from the black. It would be an obvious assumption that this presents different temperatures in the left and right sides. During the various burns, however, we noticed that both chimneys had moments when they were too cool, and others when they were both at functional temperatures. It is more likely we are looking at the results of differing ozygen levels during the time that the furnace was sintering. It is likely that we can address this by adjusting the air inlets through a separate experiment series.
Photos
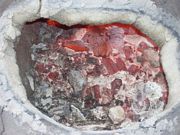 |
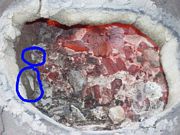 |
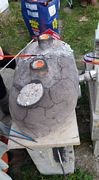 |
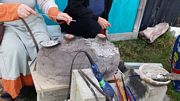 |
Charcoal |
Inlet ports |
End view |
Central view |
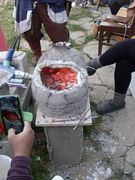 |
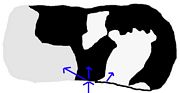 |
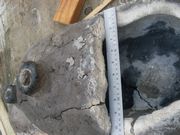 |
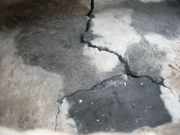 |
Open to reload |
Burn Pattern |
Overview of loading port |
Colours on the base |
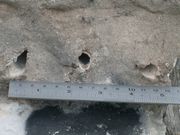 |
| | |
Inside air ports |