Iron Smelt - Wareham, ON - Nov 5, 2011
Date:Nov 5, 2011
Location:Wareham, ON
See also: Darrell Markewitz's ironsmelting site
Team: Neil Peterson, Darrell Markewitz, Ian Fleming, Lloyd Johnson
Premise: Second pass at Slag Pit but with better ore
Furnace Design
Type | Norse short shaft cobb construction, tap arch |
Extraction | top |
Diameter | 25 cm |
Height | 55 cm |
Volume | 26984.375 cm3 |
Tuyure Type | ceramic tube |
Tuyere height from base | 12 cm |
Tuyere penetration into furnace | 5 cm |
Tuyere angle | 22 deg |
Base design | slag pit - 39cm deep, tapering from 28.5 to 26cm in diameter cm |
Burn Details
Bellow Type | blower |
Avg Air rate | 900 litres per minute |
Total Charcoal Mass | 49 Kg |
Avg Burn rate | 12 min per 2 Kg |
Ore Type | taconite |
Total Mass of Ore | 19.2 Kg |
Burn Duration | 5:30 Hours |
Results
Mass of Bloom | 6.405 Kg |
Bloom Type | |
Yield | 33% |
Notes | |
 |
Reports of all of our iron smelting efforts along with more articles and information are available on the "Iron Smelting in the Viking Age" CD from the Wareham Forge. Copies of the CD can be purchased here. |
Discussion:
Conclusions:
This experiment builds on the system profile from October 8. As was suspected, the general layout of the pit and furnace combination proved workable. The shift to a iron rich ore completed the mechanism, the proof being in a high yield of nicely dense, forgeable iron bloom.
The operation of the furnace was virtually flawless. At no time was any significant liquid slag observed at the tuyere, with no interuption of air. Intentionally the consumption rate was kept to the 10 - 12 minute per standard (1.8 kg) charcoal measure. This was because of a concern the pure taconite ore might tend to produce a high carbon cast iron otherwise.
One other result was that the furnace itself has proven both stable and durable. After the smelt, the body of the furnace was carefully placed on wooden planks, then slid off to one side of the smelt area. After the slag block was excavated, the retaining walls were replaced, the pit filled with earth / ash / slag mixture. With the furnace body slid back into place, there is no reason that another smelt could not be undertaken using the same structure. Noteably, the ceramic tuyere, which at this point has endured three separate full smelts, shows every sign of being able to withstand yet another.
Photos:
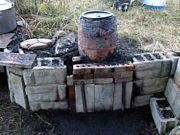 |
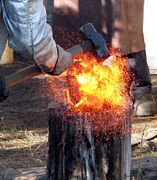 |
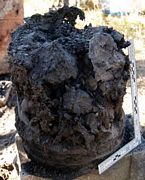 |
|
Smelter Setup |
Big Bloom |
Slag block |
Raw Data:
CLOCK |
ELAPSED |
EVENT |
AIR |
|
|
CHARCOAL |
|
|
ORE |
|
|
|
|
|
|
|
|
UNIT |
COUNT |
TOTAL |
UNIT |
COUNT |
TOTAL |
|
|
|
gage |
LpM |
P |
bucket |
|
kg |
scoop |
kg |
kg |
|
|
|
|
|
|
|
|
|
|
|
0.28 |
12:00 |
|
start bark pieces pre-heat |
3 |
300 |
|
|
|
|
|
|
|
12:50 |
:50 |
fill with rough charcoal |
8 |
800 |
|
3 |
3 |
|
|
|
|
13:15 |
:25 |
reaction column hot |
|
|
|
|
|
|
|
|
|
13:20 |
(1:20) |
pre-heat complete |
|
|
|
3 |
6 |
10.80 |
|
|
|
|
|
|
|
|
|
|
|
|
|
|
|
12:00 |
|
main sequence start |
|
|
|
|
|
|
|
|
|
12:10 |
:10 |
graded charcoal |
|
|
|
1 |
7 |
|
|
|
|
12:23 |
:13 |
|
|
|
|
1 |
8 |
|
|
|
|
12:34 |
:11 |
|
|
|
|
1 |
9 |
|
|
|
|
12:45 |
:11 |
finish 8.5 kg / increase air |
9 |
900 |
|
1 |
10 |
8.50 |
|
|
|
12:51 |
|
first ore addition |
|
|
|
|
|
|
at 3/4 |
|
|
13:00 |
:15 |
|
|
|
|
1 |
11 |
|
|
1 |
1 |
13:11 |
:11 |
|
|
|
|
1 |
12 |
|
|
1 |
2 |
13:22 |
0:11 |
|
|
|
|
1 |
13 |
|
|
1 |
3 |
13:34 |
0:12 |
|
|
|
|
1 |
14 |
|
|
1 |
4 |
13:45 |
0:11 |
finish 8.75 kg |
|
|
|
1 |
15 |
17.25 |
|
1 |
5 |
13:58 |
0:13 |
|
|
|
|
1 |
16 |
|
|
1 |
6 |
|
|
increase ore amount |
|
|
|
|
|
|
at 1.25 |
|
|
14:10 |
:12 |
|
|
|
|
1 |
17 |
|
|
1.5 |
7.5 |
14:22 |
0:12 |
finish 6.75 |
|
|
|
1 |
18 |
24.00 |
|
1.5 |
9 |
14:34 |
0:12 |
|
|
|
|
1 |
19 |
|
|
1.5 |
10.5 |
14:42 |
0:08 |
|
|
|
|
1 |
20 |
|
|
1.5 |
12 |
|
|
increase ore amount |
|
|
|
|
|
|
at 2 |
|
|
14:51 |
:09 |
|
|
|
|
1 |
21 |
|
|
2 |
14 |
14:58 |
0:07 |
|
|
|
|
1 |
22 |
|
|
2 |
16 |
15:07 |
0:09 |
finish 9 kg |
|
|
|
1 |
23 |
33.00 |
|
2 |
18 |
15:13 |
0:06 |
all ore added |
|
|
|
1 |
24 |
|
|
1.2 |
19.2 |
15:17 |
|
reduce air |
8 |
800 |
|
|
|
|
|
|
|
15:24 |
:011 |
|
|
|
|
1 |
25 |
|
|
|
|
15:31 |
0:07 |
final charcoal added / burn down |
|
|
|
1 |
26 |
38.40 |
|
|
|
15:41 |
|
reduce air |
5 |
500 |
|
|
|
|
|
|
|
|
|
|
|
|
|
|
|
|
|
|
|
16:00 |
|
approximate extraction time |
|
|
|
|
|
|
|
|
|
|
|
|
|
|
|
|
|
|
|
|
|
|
|
TOTALS |
|
|
|
|
|
|
|
|
|
|
|
|
|
|
|
|
|
|
|
|
|
|
TIME |
pre-heat |
1:20 |
hrs |
|
|
|
|
|
|
|
|
|
main sequence |
4 |
hrs |
|
|
|
|
|
|
|
|
|
TOTAL |
5:30 + |
hrs |
|
|
|
|
|
|
|
|
|
|
|
|
|
|
|
|
|
|
|
|
ORE |
TOTAL - taconite |
19.2 |
kg |
|
|
|
|
|
|
|
|
|
|
|
|
|
|
|
|
|
|
|
|
CHARCOAL |
rough |
10.8 |
kg |
|
|
|
|
|
|
|
|
|
graded |
38.4 |
kg |
|
|
|
|
|
|
|
|
|
TOTAL |
48.4 |
kg |
|
|
|
|
|
|
|
|
|
|
|
|
|
|
|
|
|
|
|
|
BLOOM |
TOTAL |
6.4 |
kg |
|
|
|
|
|
|
|
|
|
YIELD |
33 |
% |
|
|
|
|
|
|
|
 |
Reports of all of our iron smelting efforts along with more articles and information are available on the "Iron Smelting in the Viking Age" CD from the Wareham Forge. Copies of the CD can be purchased here. |